Contents
- 1 How Is 3D Printing Used in Electronics Enclosure Design?
- 2 Why Do Custom Enclosures Matter in Electronics?
- 3 What Are the Benefits of 3D Printing for Custom Enclosures?
- 4 What Are the Challenges of Using 3D Printing for Custom Enclosures?
- 5 Best Practices for Designing 3D Printed Enclosures
- 6 Real-world Applications of 3D Printed Enclosures
- 7 The Future of 3D Printed Enclosures in Electronics Manufacturing
- 8 Conclusion
How Is 3D Printing Used in Electronics Enclosure Design?
Overview of 3D Printing Technology in Electronics
3D printing is used across industries, including electronics. It’s most commonly used for rapid prototyping—allowing designers to quickly create and test mockups to verify designs and functionality. This means quicker production and time-to-market, as designing, printing, and testing can be achieved at a significantly faster pace.
As a result, product development is advantageous for consumer electronics. It also significantly reduces costs compared to traditional manufacturing methods, often by consolidating multiple parts into a single, cohesive unit.
Manufacturers use 3D printing, with materials like PLA and ABS, to produce lightweight, durable electronic enclosures.
As this technology can form complex geometries, you can easily integrate chips, sensors, and other components into the enclosure.
And given its speed, you can easily verify the exact measurements needed to house the device.
Why Do Custom Enclosures Matter in Electronics?
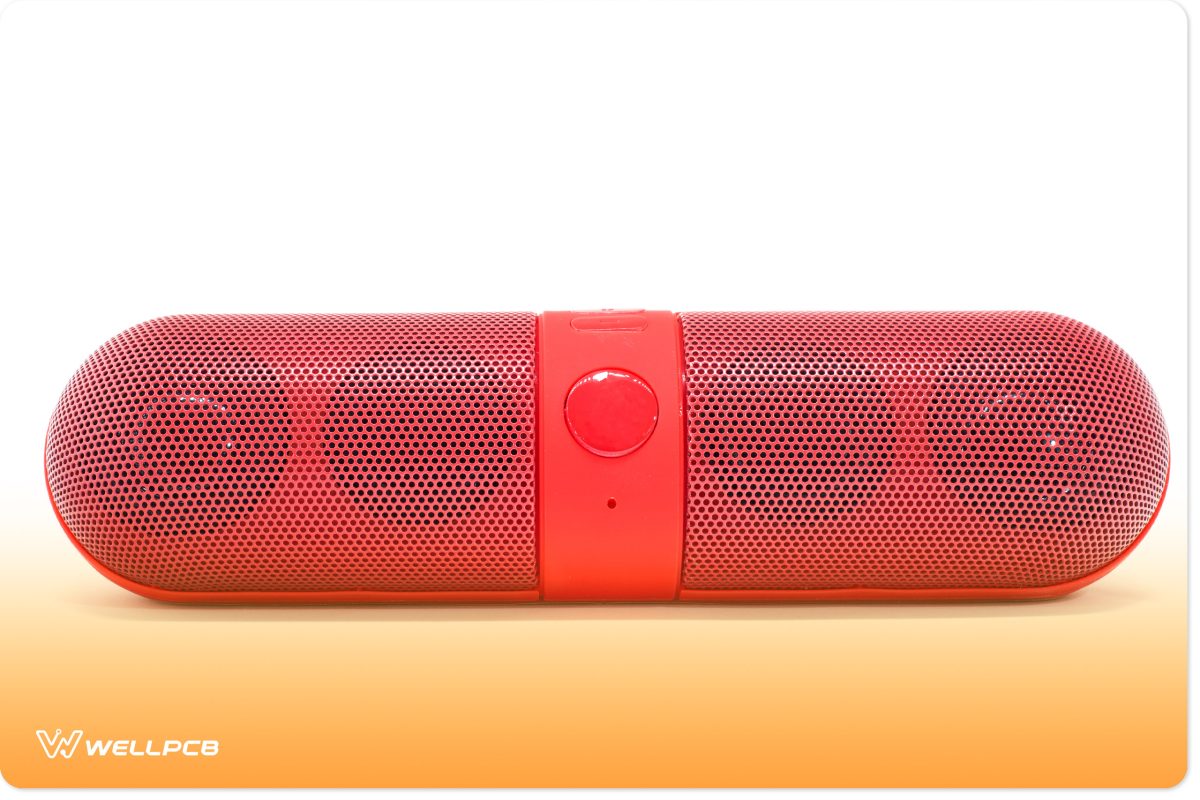
Custom enclosures protect electrical components, including circuits, from dust, moisture, physical impact, and other hazards that could compromise performance or safety.
They also prevent electric shocks, making devices safer for users and extending their lifespan.
With consumer electronics trending towards sleek, thin, and touch-screen-compatible devices, enclosures need to meet specific aesthetic and functional standards.
An attractive, well-designed enclosure can enhance a product’s appeal.
Custom shapes and designs—whether complex or simple—are also easily fabricated.
Engineers leverage this technology to improve component placement and designs, leading to a better overall customer experience.
Adding ventilation systems, for instance, can make a device easier to handle safely and improve interactivity.
By embracing 3D printing, businesses can improve performance and marketability while reducing costs.
What Are the Benefits of 3D Printing for Custom Enclosures?
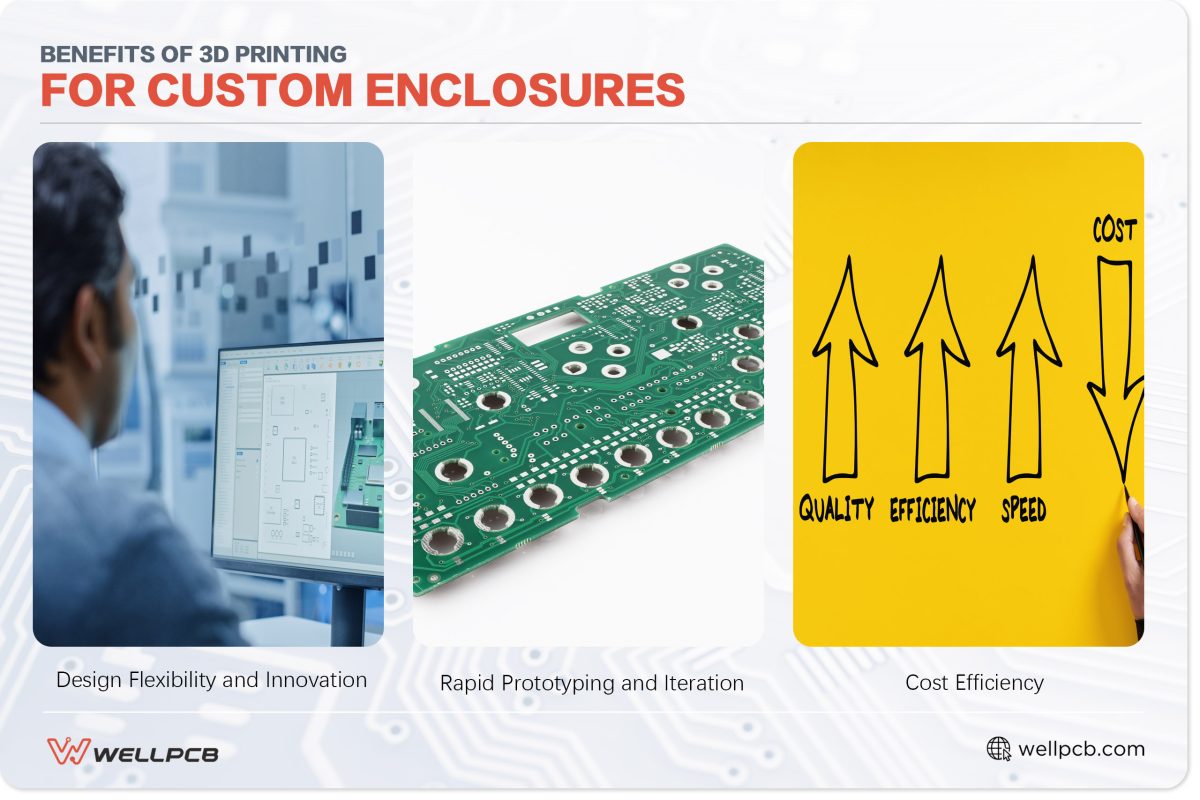
Design Flexibility and Innovation
3D printing allows product developers to create unique enclosure designs that would be difficult—or even impossible—to achieve with traditional manufacturing techniques like CNC machining. Examples of such design possibilities include:
- Enclosures made of different materials: Manufacturers can combine materials to create enclosures with unique features like soft-touch surfaces, rigid structures, or flexible sections. This versatility is ideal for wearables, which need both durability and comfort.
- Cooling and ventilation: Enclosures can feature cooling channels for devices that generate and accumulate heat, such as high-performance computers and other devices. By facilitating effective heat dissipation, these designs can significantly improve lifespan and functionality.
- Customized sizes: 3D printing enables the creation of custom-sized enclosures that fit specific devices or components. This provides better protection and reduces wasted space—vital for medical devices and consumer electronics. Hearing aids, for example, require custom enclosures that can influence sound quality and feedback.
- Topology optimization: By optimizing the topology, manufacturers can develop lightweight, high-strength enclosures with lattice-like structures that reduce weight without sacrificing durability. Industries like aerospace use this technology to produce complex engine parts with efficient cooling channels that boost performance.
Rapid Prototyping and Iteration
With 3D printing, businesses can rapidly create and test enclosure iterations before approving the final design. This is more cost-effective than standard manufacturing and enables quicker prototype production. In just hours or days, companies can print an enclosure, assess its form, fit, and function, and then adjust the design based on testing and feedback.
Manufacturers can also adjust the design based on testing or feedback received. This allows businesses to reduce errors and optimize materials, features, and structural designs before moving on to mass production.
One example is Engineered Profiles, which developed a 3D-printed tool for a trade show. Production took place within a single night, and the customer was able to test and approve the design without financial risk. Using this method, they were able to accelerate the design process and cut costs, finalizing 90% of the design before printing the tool.
Cost Efficiency
3D printing significantly reduces costs for low-volume production runs. With each part printed independently, costs remain consistent regardless of volume—making it a cost-effective alternative to injection molding.
For example, manufacturing 100 enclosures via injection molding can easily cost up to $10,000 for the mold alone. In contrast, 3D printing the same quantity would only cost between $1,500 and $3,000.
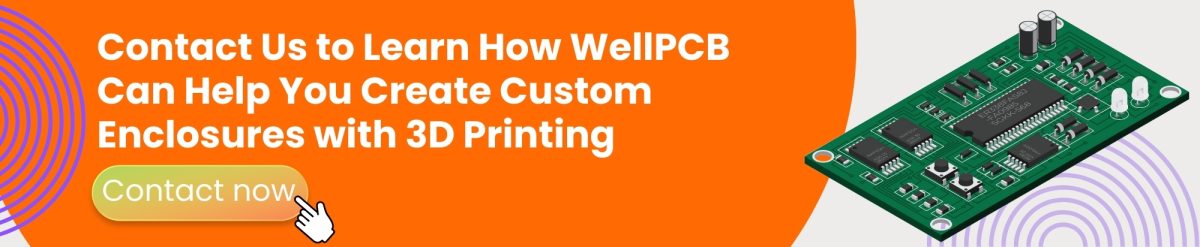
What Are the Challenges of Using 3D Printing for Custom Enclosures?
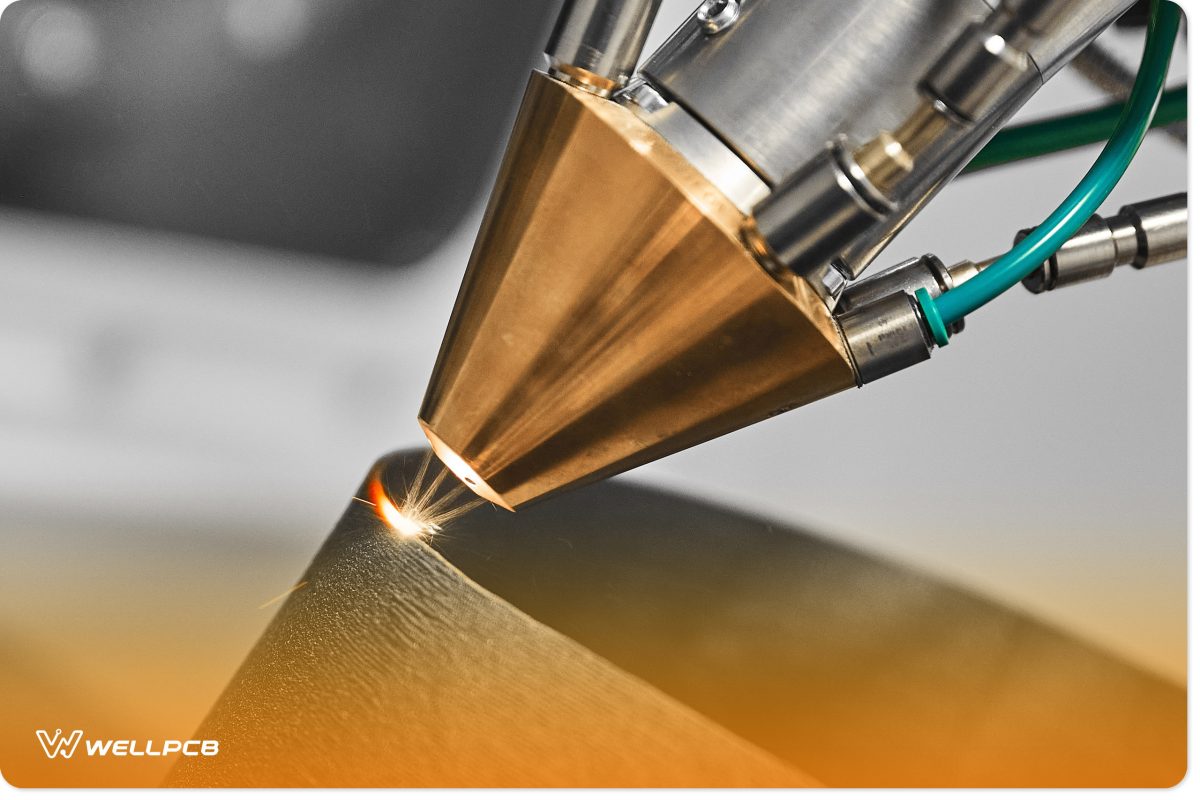
Material Selection and Durability
Choosing the right material is crucial for durability, heat resistance, and electrical insulation. That said, each material has trade-offs.
- Durability: Enclosures often need to withstand mechanical stress, impact, and wear. Materials like Nylon and ABS are generally durable, but some applications may require even tougher options.
- Heat resistance: Devices that generate significant heat require enclosures made from heat-resistant materials. For instance, PLA, while easy to print, has a low melting point and may warp in high temperatures. As such, a material like polycarbonate is a better choice for heat stability.
- Electrical insulation: Effective electrical insulation prevents short circuits and protects sensitive components. Materials like PETG and ABS are commonly used as they offer electrical insulation. However, careful consideration is needed for components that are sensitive to even small amounts of conductivity.
Different materials offer specific advantages:
- ABS: Strong, lightweight, and impact-resistant, though it releases fumes during printing.
- PETG: Flexible, an electrical insulator, and resistant to chemicals but can be difficult to print due to stringing.
- PLA: Easy to print with a smooth surface finish, but unsuitable for high-heat applications.
Achieving Precision and Quality
Ensuring a high-quality, precise finish in 3D printing is a common challenge.
- Surface finish: Printed enclosures may have visible layer lines, which can impact aesthetics and functionality. Smooth finishes are often essential for assembly.
- Accuracy: The enclosure’s dimensions should match the design—this is crucial for component fitting and assembly. Improper fitting usually stems from errors in extrusion, layer alignment, or material flow.
- Material shrinkage: Certain materials shrink during the cooling process, which can lead to design inaccuracies in the final product.
To ensure precision and quality, follow these tips:
- Set layer height to 0.1mm or less for fine detail.
- Calibrate the printer thoroughly and set speeds to 30–50mm/s.
- Use a 0.25mm nozzle diameter for intricate designs.
- Sand, polish, or fill in small gaps to achieve a smooth finish.
Scalability for Mass Production
When scaling 3D printing for large-volume production, you may face several limitations.
- Production speed: 3D printing is slower than injection molding, particularly for large orders. The layer-by-layer process can make mass production time-intensive, even when using multiple printers simultaneously. Taking days or weeks to complete large orders makes this approach unsuitable for companies requiring short lead times.
- Consistency: Ensuring all enclosures are developed consistently can be challenging. Factors like printer calibration, environmental conditions, and filament quality can introduce inconsistencies.
3D printing excels at prototyping and small-batch production. Designers can create different enclosure iterations before deciding on a final production design.
As it doesn’t require molds, businesses can achieve cost-effective small-batch production of enclosures that meet specific requirements.
However, for large-scale production, injection molding may be more suitable due to its lower per-unit cost after mold creation.
Best Practices for Designing 3D Printed Enclosures
Design Considerations
To create effective 3D-printed enclosures, follow these guidelines to ensure optimal functionality, ease of assembly, and component protection:
- Ensure enough space for all internal components to fit comfortably without crowding. This helps prevent damage during assembly and future use.
- Make a template of the internal components to guide design decisions and ensure all parts fit properly inside the enclosure.
- Include secure mounting points for batteries, sensors, or PCBs to prevent movement within the enclosure.
- Add ventilation slots near heat-generating components to facilitate cooling, but make sure these slots do not compromise the structure.
- For enclosures containing sensitive electronics, consider adding mounts for fans to enhance cooling.
- Add lips and lugs at joining points to improve assembly precision and structural stability.
- Use snap-fit mechanisms for parts that require frequent assembly and disassembly.
- Design the enclosure so that all parts can be assembled from a single direction, ideally vertically, to simplify construction.
- For parts that may require frequent access or replacement, add sliding faces, screws, or flexible lugs to enable easy access.
Material Selection
Materials have unique properties that make them suited to specific enclosure applications. Here’s a quick guide:
Material | Flexibility | Strength | Thermal & Key Properties | Use Cases |
Polycarbonate | Low flexibility | Very strong | High heat resistance (110°C) | Automotive, aerospace, demanding applications |
Nylon | Moderate flexibility | Rigid and strong | High heat resistance (180°C), impact and wear-resistant | Moving parts, industrial enclosures |
PLA | Fragile | Durable and strong | Low heat resistance (60°C), biodegradable, easy to print | Prototypes, indoor enclosures, concept models |
ABS | Low flexibility | Durable and tough | Moderate heat resistance (100°C), impact-resistant | Working prototypes, automotive parts, consumer electronics |
PETG | Moderate flexibility | Strong | Moderate heat resistance (80°C), water and chemical-resistant | Snap-fit components |
TPU | High flexibility | Impact-resistant | Low heat resistance (80°C), excellent vibration absorption | Flexible enclosures, wearables |
Follow these guidelines to determine when to use the material:
- Flexibility: TPU or nylon are great shock absorbers for enclosures.
- Durability: Nylon is ideal for enclosures needing impact resistance and strength.
- Electrical insulation: ABS or polycarbonate provides effective electrical insulation.
- Thermal resistance: Polycarbonate performs well in high-heat environments.
Testing and Quality Assurance
Quality assurance is essential to confirm that 3D-printed enclosures meet safety, functionality, and durability standards. Without rigorous testing, the product may fail due to component misalignment, poor heat dissipation, or structural weakness.
To test the functionality and durability of a 3D-printed enclosure, follow these best practices:
- Ingress Protection (IP): These tests determine whether the enclosure can prevent moisture, dust, and water from entering the device.
- Temperature and humidity: Ensures stable performance in various environmental conditions.
- Vibration and shock: Verifies that the enclosure can handle expected levels of shock and vibration.
- Fatigue testing: Determines if the enclosure can handle repeated or continuous stress.
- Drop testing: Tests resilience to accidental drops or impacts.
- Component placement: Checks that all internal components align correctly within the enclosure.
- Visual inspection: Confirms that the printed product meets design specifications and quality standards.
Key testing metrics include:
- Finite Element Analysis (FEA): Predicts how the enclosure performs in different environments.
- Heat Deflection Temperature (HDT): Measures warping or bending under heat and pressure.
- IP rating: Confirms that the enclosure meets industry-standard ingress protection levels.
Real-world Applications of 3D Printed Enclosures
Case Study 1: Enhancing Product Aesthetics in Consumer Electronics
Engineer Ken Pillonel used 3D printing to create an open-source electronic enclosure for Apple’s AirPods, featuring a transparent exterior and a USB-C port.
Users can easily replace the battery and access internal components, making it more repairable and extending the product’s lifespan.
By enabling longer use and reducing costs, this innovation also addresses electronic waste, making the enclosure more sustainable.
Case Study 2: Custom Enclosures for Medical Devices
In the medical field, 3D printing is used to create custom enclosures for surgical guides.
Made with biocompatible materials, these enclosures improve surgical precision by allowing surgeons to use optimal angles and incision locations.
As a result, implants are correctly inserted based on pre-surgery templates. This reduces surgery time, improves patient outcomes, and minimizes complications.
3D printing also speeds up regulatory approval by supporting rapid prototyping and design refinement, significantly reducing time-to-market for new medical devices.
The Future of 3D Printed Enclosures in Electronics Manufacturing
Emerging Trends and Innovations
- Advanced materials: 3D-printed enclosures are being developed using new materials with enhanced properties, including higher thermal resistance, greater strength, and improved flexibility. Engineers now have access to conductive filaments, biocompatible materials, and carbon fiber-reinforced polymers, each providing unique advantages. These innovations have seen growing applications in the medical, aerospace, and electronics industries, where they support specialized requirements for durability, safety, and functionality in electronics enclosures.
- Multi-material printing: 3D printers can now combine multiple materials into one enclosure, allowing for more complex designs and enhanced functionality.
- Smart enclosures: Enclosures with integrated circuits, antennas, or sensors are becoming popular, especially in IoT applications. These smart enclosures add capabilities like data collection, connectivity, and real-time monitoring, providing added value and protection.
These trends support more customizable, efficient, and cost-effective electronic enclosures.
After all, rapidly prototyping with different materials encourages innovation and significantly faster product development.
Potential Industry Impact on the Industry
- Customization: 3D printing enables mass customization that’s cost-effective at scale. For instance, manufacturers can print personalized enclosures without needing to retool. This is especially valuable for medical devices and consumer electronics, where custom designs directly improve functionality and user experience.
- Innovation: 3D printing gives manufacturers far greater design freedom, allowing for lightweight, complex enclosures with unique shapes, textures, cooling features, and sensor integration. This flexibility is set to inspire the development of new electronic products and groundbreaking designs.
- Sustainability: By minimizing material waste and enabling the use of biodegradable polymers, 3D printing supports more sustainable electronics manufacturing practices. Businesses adopting this technology can reduce their environmental impact and contribute to sustainability goals.
Conclusion
3D printing for custom electronics enclosures offers significant benefits, including cost savings and faster time-to-market compared to traditional manufacturing.
And as it allows for multiple materials to be used within one enclosure, it offers improved strength, flexibility, and long-term durability.
However, it also has several key limitations, such as slower production speeds for large volumes and challenges in material selection and surface finishing.
For expert assistance and to explore our 3D printing services, contact WellPCB. We’re ready to bring your next project to life with precision and expertise.
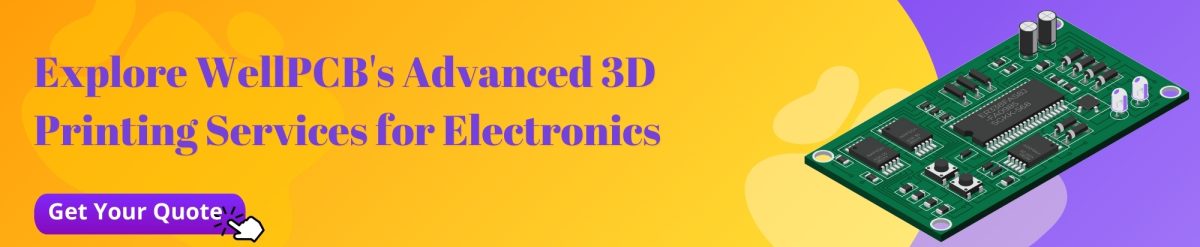