Contents
Provides Complete Protection
Conformal coatings protect circuit boards from humidity, dust, fungus, extreme temperatures, and other contaminants.
Recently, there has been a higher demand for PCBs that withstand extreme environmental conditions. As a PCB designer, you must follow this trend and make PCBs that are durable and reliable in such terms; hence, conformal coatings.
This coating provides resistance to various chemical attacks, such as corrosion. Without a conformal coating, your PCB is at risk, and some fragile components can be damaged during exposure to extreme temperatures.

Extend the Life of PCB Board
Conformal coating not only protects a PCB to ensure reliability, but its layer of protection also expands the board’s working life, keeping costs low.
By applying conformal coatings on the surface of your PCB, the PCB will have an extended working life of up to five years and, sometimes, ten to fifteen years. Because of damage to the PCB’s vulnerable parts, it will save you from buying a new product every six months or so of costs.
The thin layer of a protective material (conformal coating) will protect your PCB from harm and give you the worth of your money and more for years to come.
PCB conformal coatings offer long-term reliability, making them an excellent option to consider during PCB assembly services.

Improves Dielectric Properties
Dielectric strength measures the conformal coating’s insulation effectiveness. Conformal coatings with high hydrophobic properties and lower extractible ionic impurities are more likely to repel water.
Hence, they have a higher dielectric strength. Applying conformal coatings to PCBs provides an extra layer of protection for your products, protecting the PCB against corrosion.

You Can Apply it Easily.
There are various ways to use conformal coatings on your PCB. The extra protection they offer makes the circuit boards durable and reliable. Some ways to apply layers include Dipping, Brushing, and Spraying.
Dipping
This technique can be used when producing many PCBs, as the coating penetrates every component. However, it is not the best technique for conformal coating, as it leads to leakage and is not suitable for many circuit boards.
As a PCB designer or an electronic engineer, if you design the PCB with Dipping as the form of coating technique during the design process, it will be more comfortable and productive.
Brushing
This technique can be used when producing a few PCBs. As the name implies, you can brush the coating on the surface of the PCB to ensure its longer life span and reliability.
You can also use the brushing technique for low volume, repairing, and finishing. One advantage of Brushing is that it causes bubbles.
However, you must have the right skill sets and experience when using this method of coating.
Spraying
You can achieve this by applying the layer to the PCB’s surface with spray bottles or guns. This is the best method to use if you produce low or medium volumes of PCB. It has more advantages than brushing and dipping.
With the right experience and skillset, Spraying is the best option for coating your PCB. However, Spraying does not allow deep penetration of some components, which can be a problem if you want the coating to reach some parts.
It saves you time, energy, and money. To prevent slumping, a common problem of Spraying, add a second layer of the coating by brushing or dipping.
For better results, use atomized Spraying, a surface that requires standing at a distance from the PCB where the sheet atomizer is complete.
Another form of Spraying is the automated method, often faster than manual. By evaluating your PCB design extensively, you will know the coating method suitable for your design.

Saves Time and Cost
Conformal coatings are cost-effective, and the various methods of using the layers save time. The application process is simple and time-effective.
Like most manufacturing processes, the application methods of conformal coating have taken a new turn in recent years; hence, the movement from manual to automatic application mode.
The application mode has shifted from dipping and spaying to selective, robotic coating processes. Depending on your budget and the quantity of PCBs you want to produce, conformal coatings are cheap and time-effective.

Protects Sensitive Information
Applying the right amount of conformal coating on your PCB can protect sensitive components from exposure to extreme temperatures.
When designing your PCB, some parts might be prone to damage. Harsh conditions like rain, dust, and heat, amongst others, can reduce the PCB’s lifespan.
Using a conformal coating on your PCB can help reduce the need for replacement or repair after a short period of use. It also protects the fragile components of the PCB.
As a PCB designer or an electronics engineer, conformal coatings to the circuit board protect the most fragile part of the board and the board’s circuits.
The protection this coating gives the printed boards extends the life of the components, the PCB, and the system you will install.
Because of the dangers attached to PCB failures, it is essential to protect the PCB’s sensitive components, hence using the conformal coating.
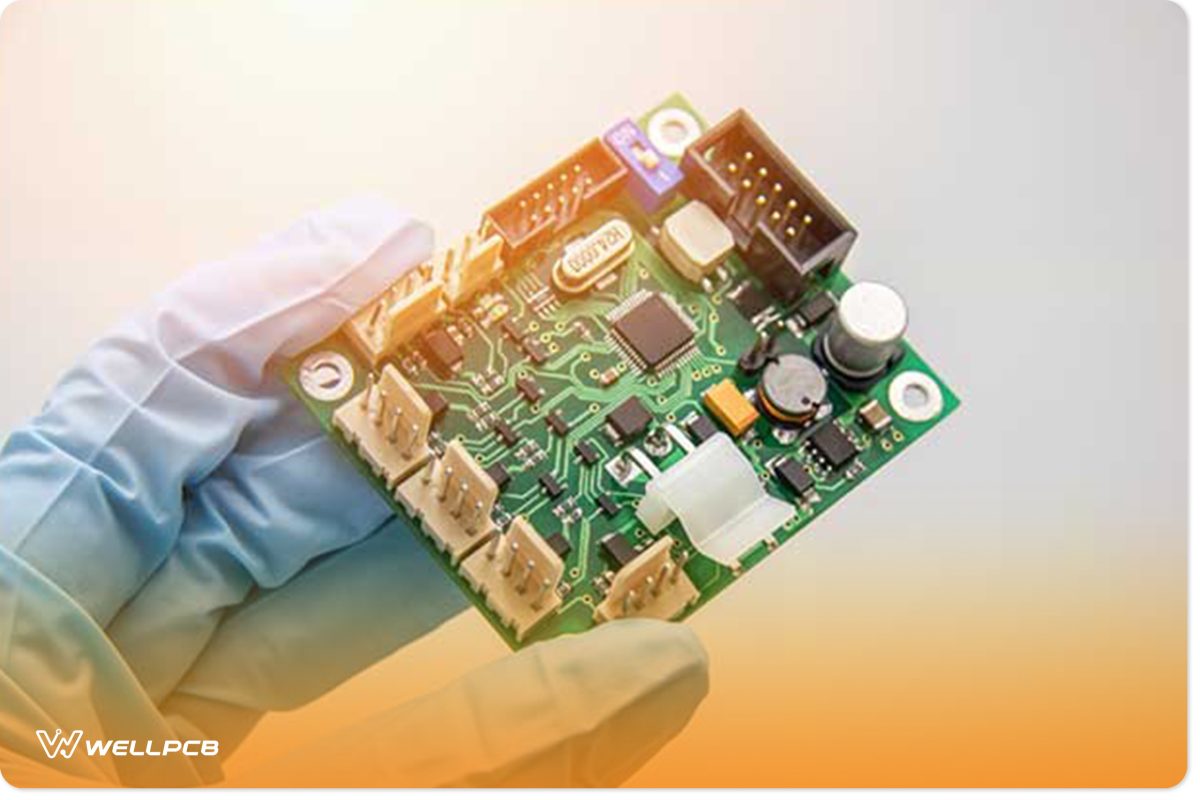
Flexibility
The conformal coating must be flexible enough to ensure that all the board’s components and parts receive sufficient layers without cracking.
Proper softness also ensures that the PCB movement from one location to another will not damage the surface.
Also, the flexibility level of conformal coating ensures that the PCB has room for expansion and contraction without cracking.
There are different conformal coatings. They include;
Acrylic resin
a conformal coating with the right level of elasticity and offers adequate protection to the PCB components.
The acrylic coating has high dielectric strength, and it is easy to remove. If you have a low budget and your finished goods will not contact solvents and other solvent vapors, you can use acrylic resin for your PCB.
Epoxy conformal coating
It provides a hard layer of protective covering for your PCB and, unlike acrylic resin, withstands humidity and corrosion.
This makes it a better option for PCBs whose end product will be susceptible to harsh conditions like heat, dust, rain, etc.
However, unlike acrylic resin, it is not very flexible and easy to remove. It can cause the PCB to crack during expansion and contraction.
Silicone resin
It protects circuit boards in extreme temperatures and is highly flexible. It prevents corrosion and withstands humidity. Because of its rubbery texture, silicone resin is not abrasion-resistant.
Also, removing silicone resin is difficult as it requires special solvents to dissolve.
Urethane resin
The provides PCB with excellent protection against humidity and corrosion. It is abrasion-resistant, and you can use it to make circuit boards susceptible to harsh environmental conditions.
It is flexible and does not cause stress on the components of the printed circuit boards. However, removing urethane resin is difficult as it requires special solvents to dissolve.

Conclusion
Using the wrong surface coating on the PCB can damage the circuit boards. It can also cause a waste of time, money, resources, and energy.
As a PCB designer or an electronics engineer, choosing the perfect coating for your PCB is essential. Choosing a conformal coating has many advantages.
It protects the circuit boards from vibration, moisture, dust, rain, heat, and other harsh conditions.
The choice of conformal coating you use for your PCB project depends on the quantity of PCB you are producing, your budget, the operating environment, and your specific standards.