Contents
The production process of Flex PCB
Double-Sided Flex PCB
The flex PCB manufacturing process follows a series of precise steps to ensure quality and functionality. Here’s a typical sequence for producing flexible PCBs:
- Cutting
- Drill Hole
- PTH (Plated Through Hole)
- Electroplate
- Pre-Processing
- Dry Film Application
- Check Position
- Exposure
- Development
- Graphic Electroplating
- Etching
- Decorating
- Surface Processing
- Cover the Film
- Pressing
- Solidification
- Immersion Nickel
- Character Printing
- Shearing
- Electrical Measurement
- Punching
- Final Inspection
- Packing
- Shipment
Each stage is essential to achieving a high-quality end product. Working with a specialized flex PCB manufacturer ensures that every step is meticulously managed, from initial cutting to final inspection, ensuring the PCB meets rigorous industry standards.
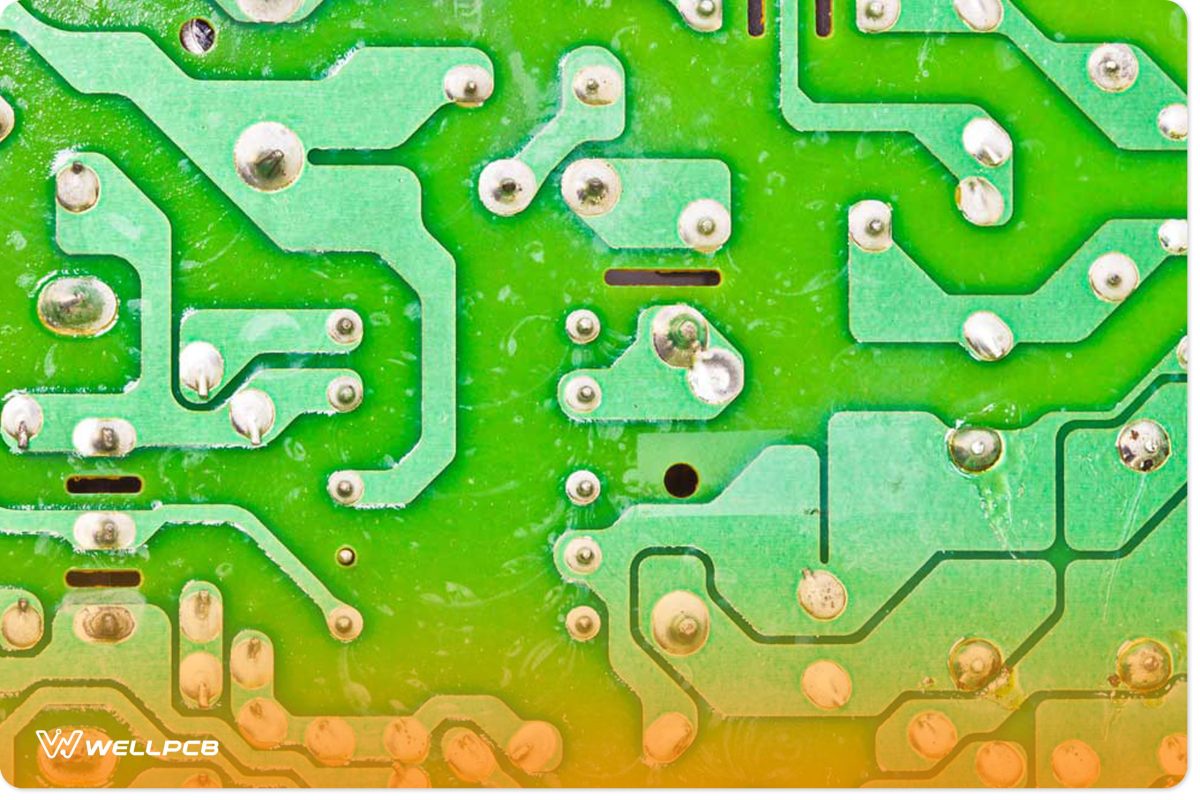
Single Panel
Cutting → Drill Hole → Dry Film → Check Position → Exposure → Development → Etching → Decorating → Surface Processing → Cover the film → Press → Solidification → Immersion Nickel → Printing character → Shear → Electrical Measurement → Punching → Final inspection → Packing → Shipment
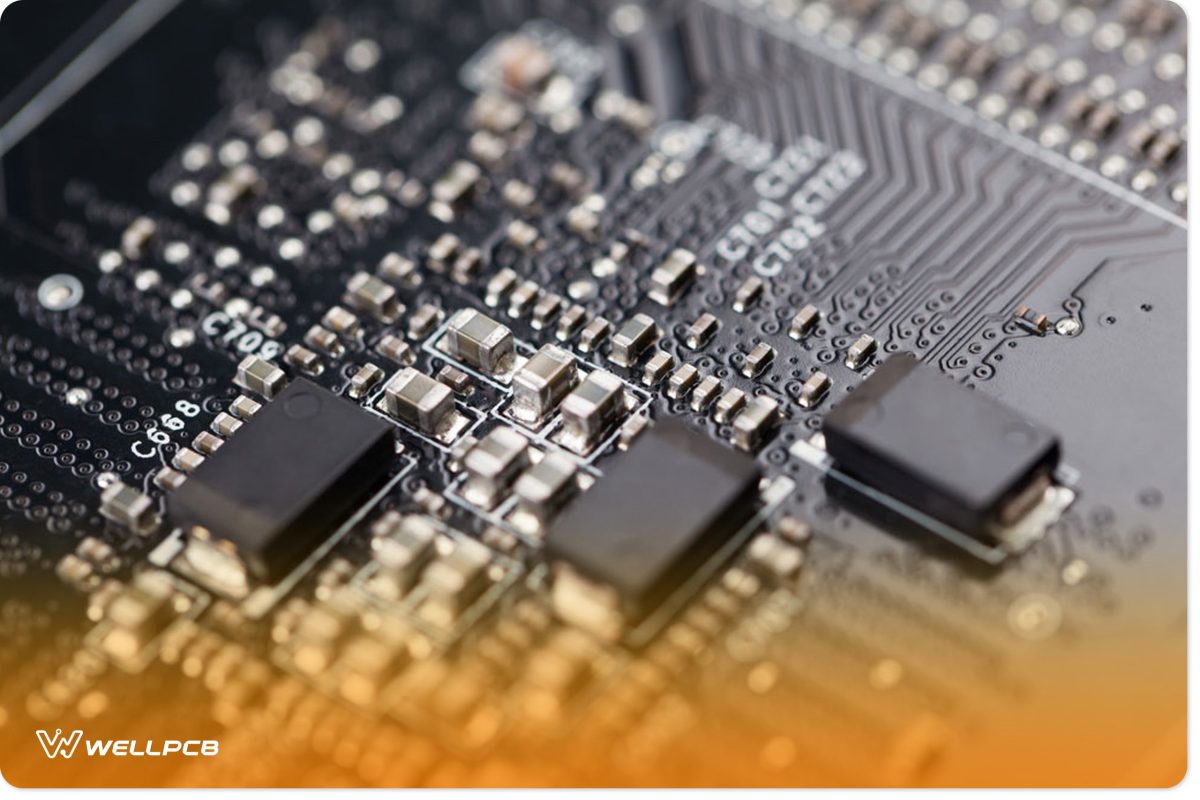
Characteristics of Flex PCB
Shorter Assembly Time: Pre-configured lines eliminate redundant cable connections.
Smaller Volume: Reduced size makes transport easier.
Lighter Weight: Lowers the weight of the final product.
Thinner Design: Enhances flexibility and supports compact, three-dimensional assembly in limited spaces.
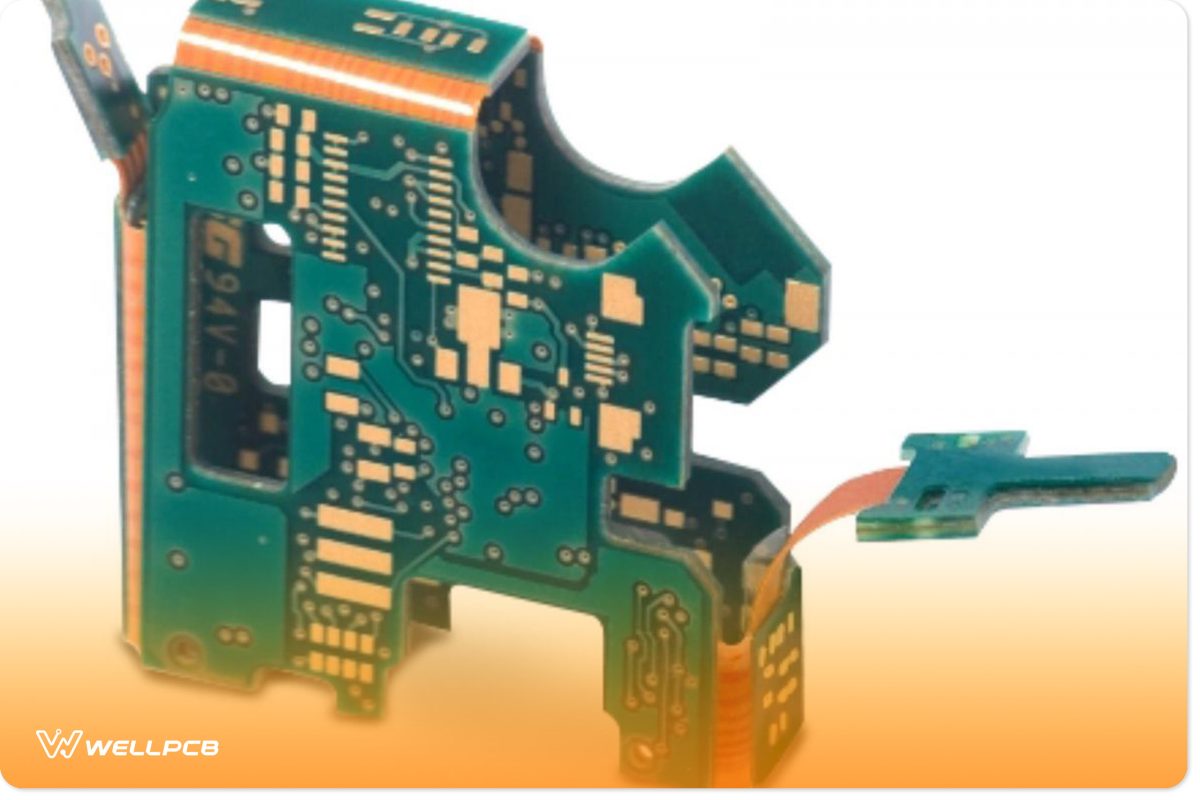
Applications of Flex PCB
Mobile phone
The thinner and lighter FPC effectively saves space while connecting the battery, microphone, and keys.
Computer and LCD screen
The Integrated Line configuration of FPC and its thickness turn digital signals into pictures displayed on the LCD screen.
CD Walkman
Thanks to the Three-dimensional assembly of FPC, overall size can be reduced.
Latest Applications:
HDD (hard disk drive) and xe encapsulation component elements.
The wireless charging coil array concentrates the electromagnetic field in a particular area to reduce space transfer consumption, thereby improving the power conversion efficiency.
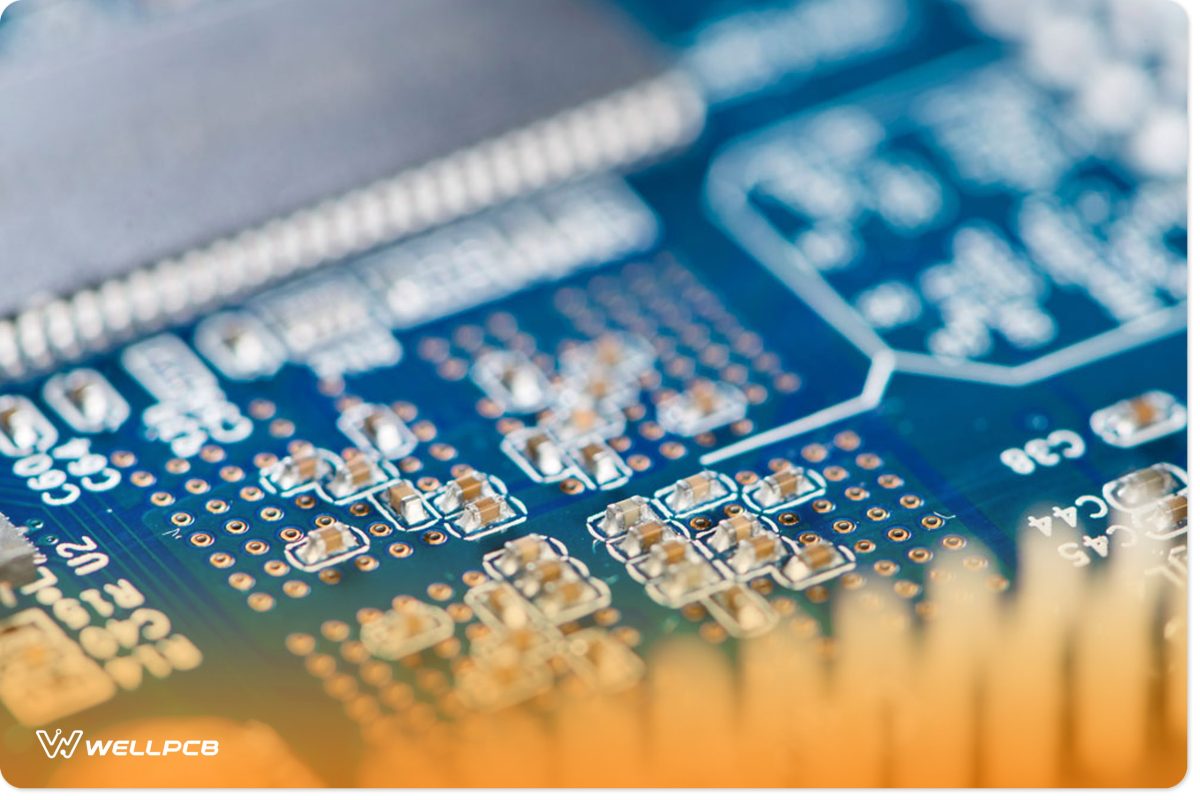
Ongoing Development of Flex PCB
For FPC to expand its applications, further development is needed in the following areas:
1. The thickness of FPC must be further reduced.
2. Folding resistance. Bending is the inherent property of FPC. Improving its strength will require better substrates.
3. The price. Far more expensive than PCB. If the price of FPC decreases, the market will be much wider.
4, Manufacturing process: The FPC process must be further enhanced to achieve minimum aperture, line width, and spacing.